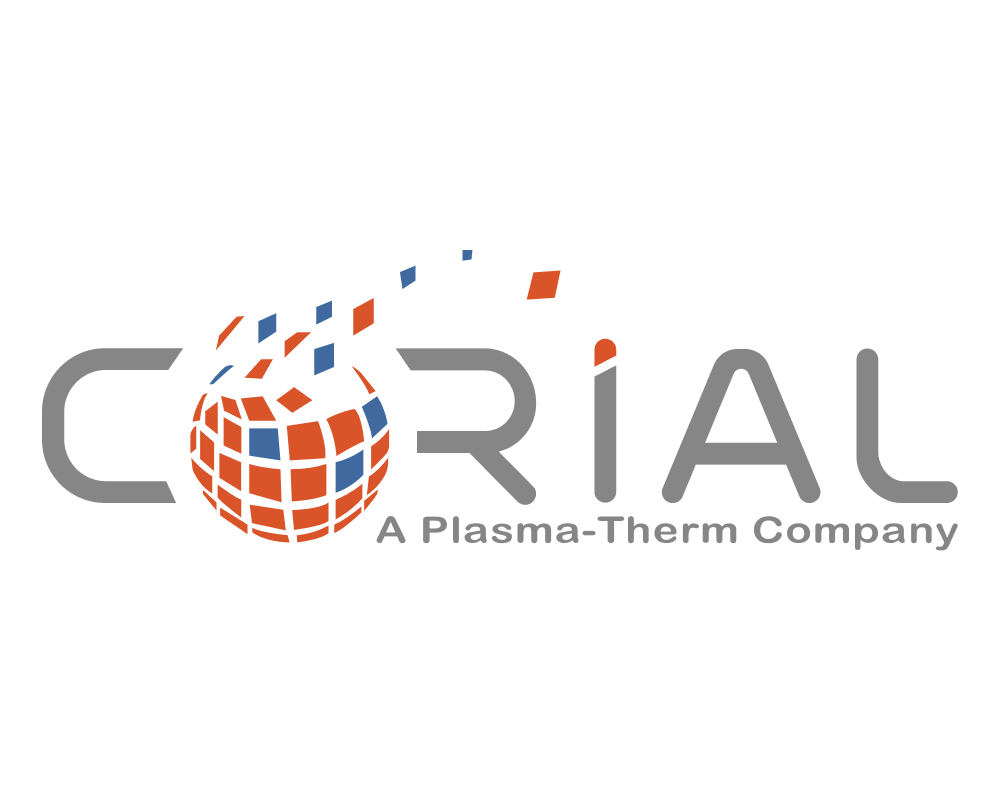
Operating for over 30 years and based in France, CORIAL is a leading equipment company that designs and manufactures plasma etch and deposition systems.
We offer innovative products and processes dedicated to the specialty semiconductor markets.
At CORIAL we have the atmosphere of a small, nimble company. The cornerstone of our philosophy is to listen, to understand your needs, and to meet the requirements of your specific applications. Our flexibility allows us to develop and manufacture equipment and process solutions designed to meet your specifications. We focus on customer support, product innovation, reliable processes, and low cost of ownership.
At CORIAL we are innovators, creators, and designers. We challenge ourselves and each other, and we believe that success is never final. We push the limit because great is not good enough.
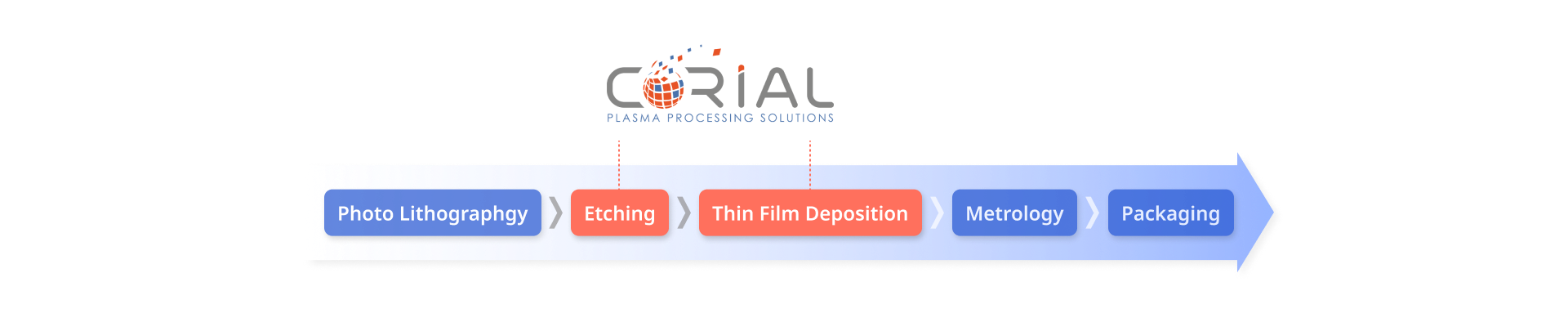
Plasma Etch (RIE / ICP-RIE)
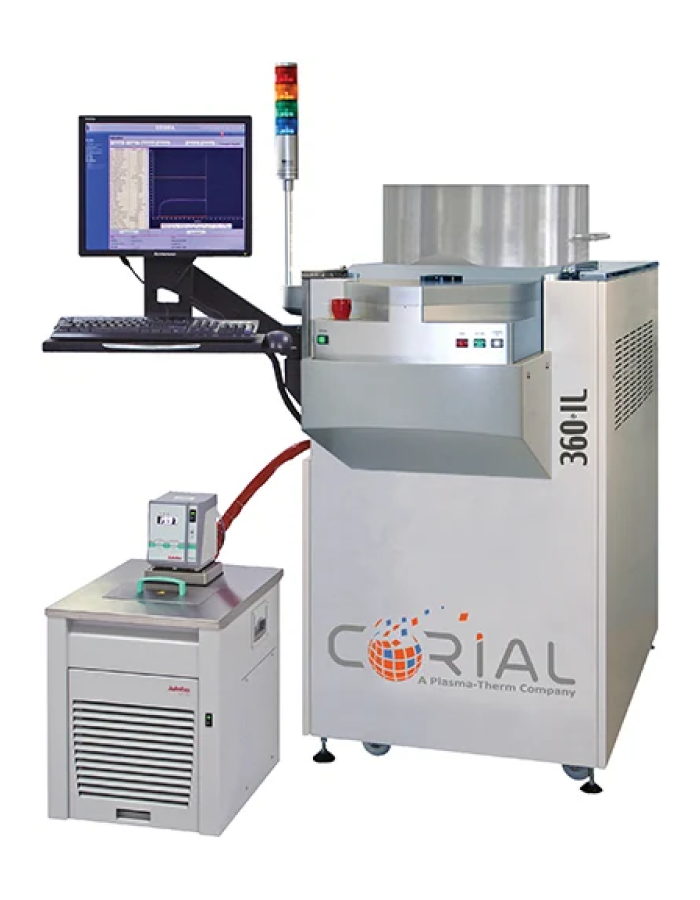
Corial 360IL
The Corial 360IL is a large area plasma etch system offering high throughput, without compromising process performance or quality.The 360IL is based on CORIAL's latest generation ICP (inductively coupled plasma) source. The system features a high-density plasma, 2 MHz ICP RF generator, and state-of-the-art gas injection, allowing fast etch rates and excellent uniformities.Featuring a vacuum load-lock, the Corial 360IL delivers stable process conditions, short pump cycles and provides the capability to run fluorinated and chlorinated based chemistries on the same tool.Our PSS processes deliver perfect conical-shaped features, even at the wafer edge, with industry leading uniformity and repeatability.For MEMS and power devices markets, the Corial 360IL ICP-RIE system is capable of processing a wide range of materials including silicon, oxides, nitrides, and III-V compound semiconductors.
Key benefits
PROCESS FLEXIBILITY
- The RF match box operating range (from 100 W to 2000 W) supports a wide range of customer applications
- The vacuum load lock enables using a combination of fluorinated and chlorinated chemistries in the same tool
HIGH ETCH RATE CAPABILITY
- Wall temperature > 250°C; ICP max power: 2000 W; RF max power: 1000 W; high efficiency of RF coupling to plasma
- Fast and uniform etching: GaAs (500 nm/min), Sapphire (75 nm/min), GaN (200 nm/min) …BEST REPEATABILITY
BEST REPEATABILITY
- Load lock for stable and repeatable process conditions
- Novel cathode design and efficient helium back side cooling of the shuttle and substrate ensure uniform temperature control (from -50°C) during the etch process
EXCELLENT UNIFORMITY
- High density plasma enables highly uniform PSS profiles
- Optimized gas showerhead with top gas inlets
OPTIMIZED LONG-LIFE SHUTTLE
- Proprietary quartz shuttle (carrier) design for PSS, with edge effect < 1 mm
- Quartz carrier lifetime > 5,000 runs
HIGH THROUGHPUT
- Large batch capacity: 23 x 2", 7 x 4", 3 x 6"
- Throughput > 8 WPH for PSS application using 4″ substrates
ICP-RIE Technology
ICP-RIE etching is based on the use of an inductively coupled plasma source.
The ICP source generates a high-density plasma due to inductive coupling between the RF antenna and the plasma. The antenna, located in the plasma generation region, creates an alternating RF magnetic field and induces RF electric fields, which energize electrons that participate in the ionization of gas molecules and atoms at low pressure. Due to the absence of an electric field near the reactor walls there is virtually no ion bombardment or erosion of the walls.
The key differentiation between ICP RIE and RIE is the separate ICP RF power source connected to the cathode that generates DC bias and attracts ions to the wafer. Thus, with ICP RIE technology it is possible to decouple ion current and ion energy applied to the wafer, enlarging the process window.
Materials are etched with the use of a chemically reactive plasma under low pressure conditions, potentially combined with ion-induced etching.
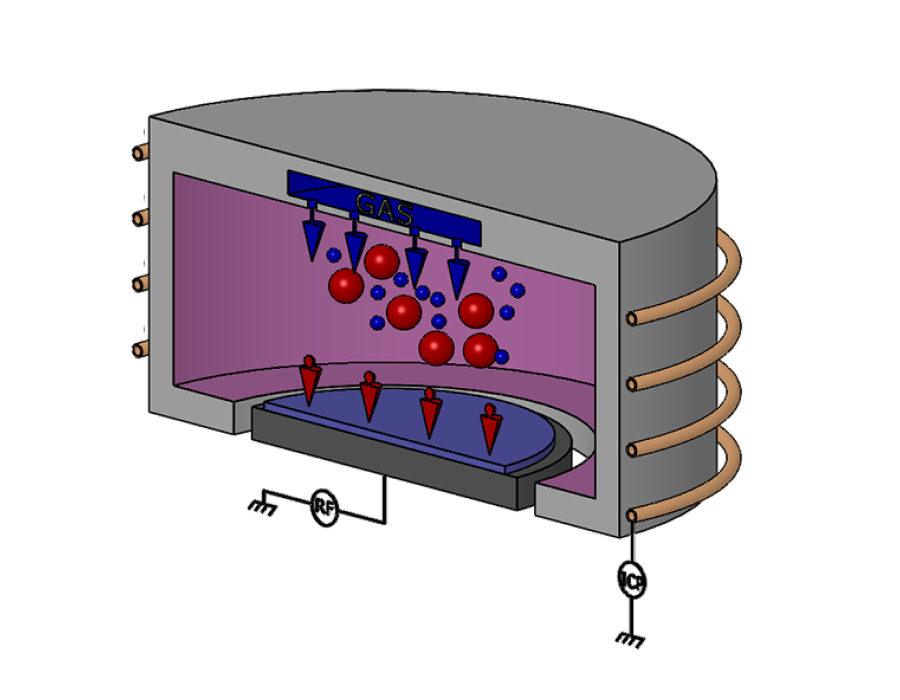
Plasma Enhanced CVD (ICP-CVD / PECVD)
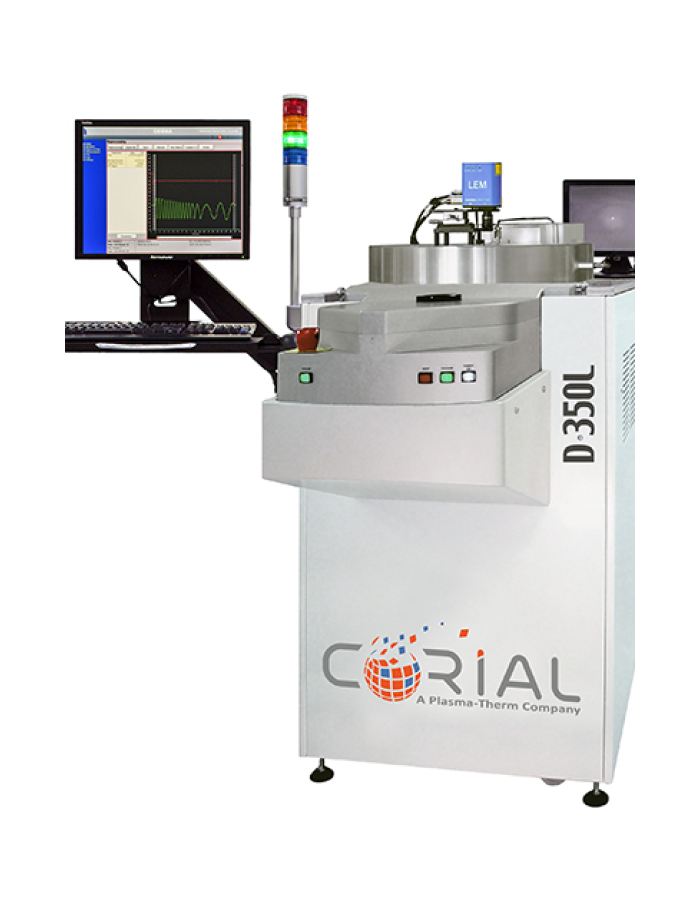
Corial D350L
The Corial D350L is based on CORIAL's unique reactor design. It houses an isothermal, pressurized reactor within a vacuum vessel, which is different from conventional PECVD reactors with heated substrate holders.
Featuring a next-generation gas showerhead and symmetrical pumping, the Corial D350L delivers excellent deposition uniformity for a wide variety of applications.
Equipped with a vacuum load lock, the Corial D350L also guarantees stable process conditions, short pumping cycles and enhanced throughput.
The Corial D350L PECVD system handles full 300 mm wafers or large batch capacity (27 x 2"), enabling volume production of high-quality films. Typical applications addressed by this PECVD tool include passivation deposition for optoelectronics, deposition of silicon oxides for photonics, and sacrificial layer deposition for MEMS. Stress control of the films is simplified and optimized on account of the symmetrical design of the reactor.
EXCELLENT UNIFORMITY
- Precise and uniform temperature control of the substrate and reactor walls delivers excellent deposition repeatability and uniformity
- The pressurized, symmetrically-pumped reactor ensures high-quality films free of pinholes
CONTROL OF FILM PROPERTIES
- Film stress control is simple to achieve, thanks to the reactor's symmetrical design
- The Corial D350L heating system enables precise control and optimization of refractive index and wet chemical etch rates
INCREASED UPTIME
- The Corial D350L high temperature, dual pumped configuration enables efficient plasma cleaning at operating temperature, with no corrosion of mechanical parts
- No manual cleaning of reactor and vacuum vessel required for many years of operation
- Load lock ensures fast loading/unloading and short pump-down times
HIGH DEPOSITION RATES
- With its isothermal, pressurized reactor, the Corial D350L rapidly deposits uniform films on wafers up to 300 mm in diameter
- Typical performance: SiO2: >500 nm/min; Si3N4: 250 nm/min; SiOCH: 150 nm/min; SiC: 100 nm/min
PECVD Technology
Plasma enhanced CVD uses RF energy at 13.56 MHz to generate, ignite, and sustain the glow discharge (plasma) between two parallel electrodes. A precursor gas mixture is introduced in the reactor and plasma is used to create reactive and energetic species by collision.
The reactive species diffuse through the sheath to adsorb on and interact with the substrate surface, and a layer of material forms on the substrate surface.
Reaction byproducts are then pumped away by the pumping system, typically comprised of a turbomolecular pump and a dry roughing pump.
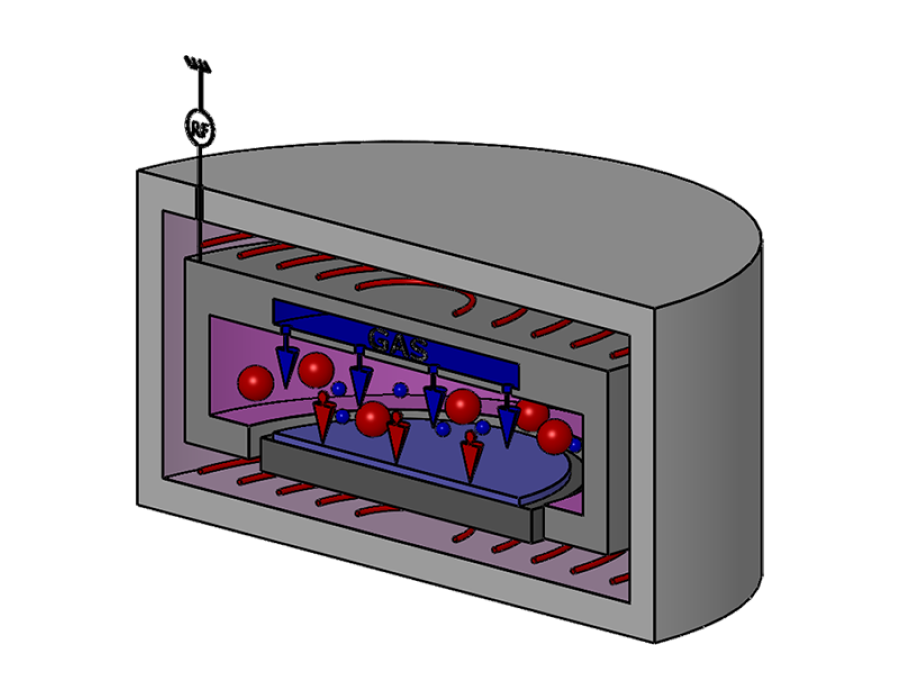
Product Line
CORIAL 200 SERIES
Systems for R&D and Small Production
- Corial 200FA RIE
- Corial 200S RIE
- Corial 200R RIE
- Corial 210RL RIE
- Corial 200I ICP-RIE
- Corial 210IL ICP-RIE
- Corial 210D ICP-CVD
- Corial D250 PECVD
- Corial D250L PECVD
CORIAL 300 SERIESSystems for 24/7 production environment
- Corial 300S RIE
- Corial 360RL RIE
- Corial 360IL ICP-RIE
- Corial D350 PECVD
- Corial D350L PECVD
CORIAL 500 SERIESVery large area batch system
- Corial D500